Common Mistakes to Avoid During PAT Testing
PAT testing is a technical process that requires a certain level of knowledge and expertise. It's not simply a matter of plugging in a device and pressing a button. Without proper training, it's easy to miss potential faults and inaccurately assess the safety of the equipment. In this article, we will highlight some common mistakes that we often see.
Not Connecting the Test Lead
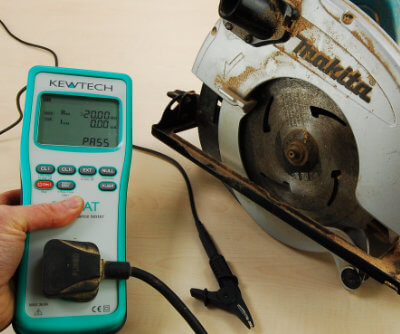
During the insulation test on Class II equipment, it is essential to connect the test lead to any exposed metal parts. Unfortunately, this is often overlooked, leading to an invalid test result. The reason why this is so common is that the test will always pass with the lead disconnected. For Class II equipment, the insulation test is measuring the resistance between the exposed metal parts of the appliance and the live conductors. Attaching the test lead is essential as it creates the return path to the PAT tester so that the resistance can be measured. If the lead is not connected, the circuit remains open, resulting in an infinitely high measured resistance, even if there is a fault. For Class I equipment, the lead does not need to be connected as the protective conductor within the cable provides the return path for the insulation resistance measurement.
Not Switching on the Appliance
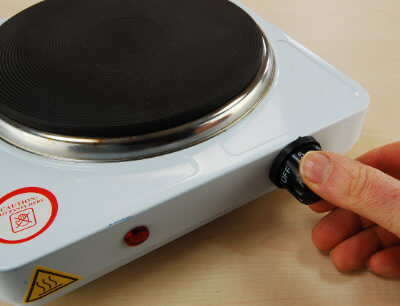
When carrying out the insulation and leakage tests, the appliance must be switched on. If the switch is in the off position during the test, the electrical circuit beyond the switch will not be tested. For instance, if the switch on a kettle is not in the 'on' position during the test, a fault with the heating element may not be identified. In some cases, the switch needs to be manually held in the 'on' position during the test.
Not Opening the Plug
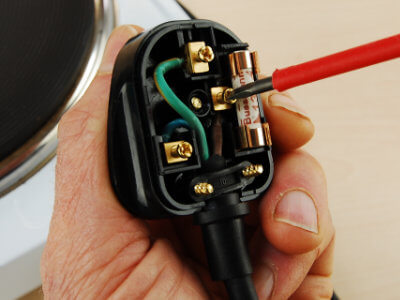
The visual inspection is the most important part of the PAT process. Most faults will be found during the visual inspection. To carry out a proper visual inspection, rewirable plugs must be opened. With the plug opened, the wiring should be checked together with the tightness of the terminals, cord grip, fuse rating, signs of overheating and any physical damage.
Assuming a 12-Month Retest Date
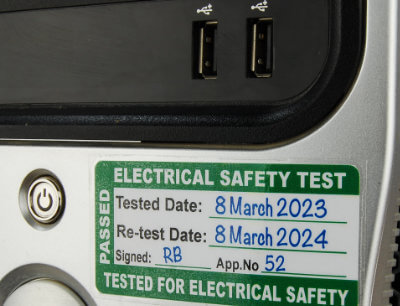
There is a persistent myth that all electrical equipment needs to be PAT tested every 12 months. This is not the case and never has been; the frequency of the inspection and testing should be based on risk assessment. Some equipment in high-risk environments may need more frequent testing and conversely, low-risk equipment does not usually require annual testing. We also have an article on assessing the frequency of the inspection and testing.
Not Recording the Test Measurement
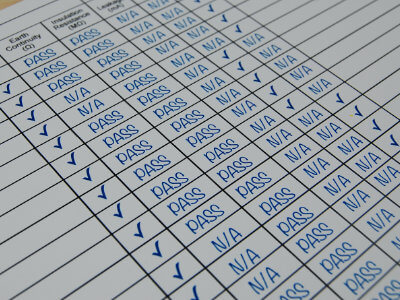
Another common mistake is to record only a 'Pass' or 'Fail' result on the test records without documenting the actual test measurement. Recording the measured value indicates that the test was correctly carried out and also provides a useful tool for identifying potential issues. For example, if an earth continuity reading increases with each subsequent test, it could indicate that the earth connection is corroding.
Attending a PAT testing course can help individuals gain the knowledge and skills necessary to perform PAT testing correctly and efficiently. A good course will cover topics such as equipment types, testing procedures, risk assessment, and proper record keeping. Participants will also have the opportunity to practice testing different types of equipment under the guidance of an experienced instructor. By investing in proper training, individuals can ensure that they are equipped with the knowledge and skills necessary to perform PAT testing correctly and effectively.