Risk Assessment Guide for PAT Testing
The frequency of the inspection and testing of electrical equipment (PAT testing) is based on a risk assessment approach. A risk assessment should be carried out to determine the likelihood of maintenance being required and the consequences of the lack of maintenance. Most organisations will likely have a mixture of environments, equipment and users. For example, a typical hotel may have different areas such as a kitchen, office, and bedrooms, each with its own unique risks that need to be assessed separately. By identifying and evaluating these risks, we can then determine the appropriate frequency of PAT testing for the equipment in each area. It is important to understand that even with regular inspections and testing, electrical equipment can still become damaged. However, through a thorough risk assessment, we can identify areas where additional control measures may be required to minimise the potential consequences of such damage. Our PAT testing course provides guidance on how to assess the risks associated with different environments, equipment, and users.
Assessment Factors
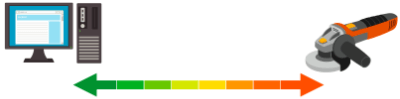
Equipment type - Some equipment types are more susceptible to damage than others. For example, small appliances are easily moved and often dropped. Large stationary appliances are rarely moved and less likely to be damaged. An electric shock from hand-held appliances is usually more serious as the fault current is more likely to pass across the heart.
We also have a separate article on equipment types.
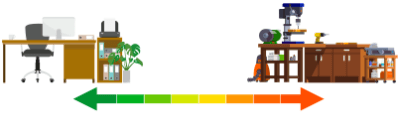
Environment - The type of environment the equipment is used in will affect the likelihood of it being damaged. Equipment used in a harsh environment, such as a construction site or industrial workshop, is more likely to be damaged than equipment used in an office. When equipment is used in a wet environment, the severity of an electric shock may be higher.
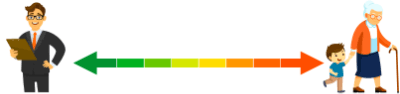
Users - Trained and informed users are likely to report damage promptly, so hazards can be avoided. Conversely, untrained users, children and members of the public are less likely to notice and report damaged equipment. For some user groups, such as children and the elderly, the consequences of an electric shock are likely to be more severe.

Equipment construction - Fault protection for Class I equipment is reliant on the integrity of the earth connection within the building’s wiring. If there is a fault in the earth circuit, the safety of Class I equipment will be compromised. Fault protection for Class II equipment is achieved by double or reinforced insulation, so there is no requirement for a connection with earth. For this reason, a Class I appliance is considered a higher risk than an equivalent Class II appliance.

Frequency of use - Equipment that is used frequently is more likely to suffer damage than equipment that is used less often.
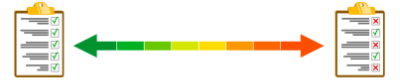
Previous Inspections - Records of previous inspection and testing may highlight which equipment is most susceptible to damage. This could be certain types of equipment, equipment used in particular environments or by a specific user type.
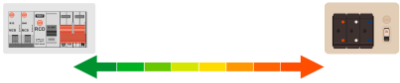
Electrical Installation - Circuits without RCD protection would be considered higher risk. The position of isolators for fixed machinery and the method of cable management should also be assessed.
Control Measures
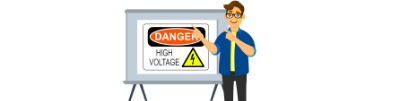
User Checks - Most faults can be found by a simple visual inspection. The user is often the person most familiar with the equipment and is in the best position to identify and quickly report faults. A user check is usually limited to an external visual check to identify typical faults such as a cracked case, damaged cable and signs of overheating. A record of any damage found during a user check will help identify any patterns of damage. Some training will be required to ensure the user has the basic knowledge and skills to conduct a visual inspection. We also have a separate article on user checks.
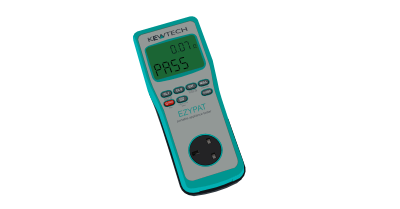
Inspection and testing - A formal visual inspection requires a detailed examination of the equipment, including opening the plug to check wiring, connections, fuse and cable grip. Testing will identify faults that can not be found by a visual inspection alone, such as a disconnected protective conductor. A PAT testing course can provide the necessary training to become competent in performing these inspections and tests and can often be done in-house by a staff member. We offer a PAT competent person course designed to equip participants with the knowledge and skills necessary to perform thorough visual inspections and tests.
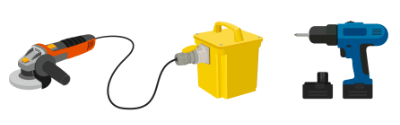
Alternative Equipment - Increasing the frequency of inspection and testing will not prevent damage from occurring if the equipment is unsuitable for the environment or its use. Where recurring damage is found, the equipment may need to be replaced with a more rugged type, or substituted with a less dangerous alternative. For example, 230V mains powered hand tools may need to be replaced with battery-powered, air-powered or 110V equivalent types.
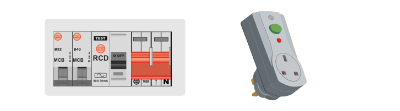
Residual Current Device (RCD) - An RCD rapidly switches off the supply if it detects a fault, reducing the potential for injury. RCDs do not detect all faults and should only be used as a secondary means of reducing the risk. Ideally, the RCD should be built into the distribution board. If this is not possible, sockets incorporating an RCD, or an RCD plug adaptor, can be used to provide additional protection.
Example Risk Based Assessments
A risk assessment can take many different forms, but essentially it is a process of evaluating the potential risks and then deciding on suitable control measures needed to reduce, minimise or eliminate any risk. The risk assessment should be regularly reviewed to ensure that the measures taken are effective and to check if there have been any changes that would affect the assessment. The Health and Safety Executive (HSE) have detailed information on creating a risk assessment.
The examples below show a basic form of risk assessment to determine a suitable frequency for the inspection and testing.
Service Engineers Van Tools & Equipment | |
---|---|
Environment | High Risk. Tools are used on customers premises. They are sometimes required to be used outdoors |
User | Staff are technically competent but they have not received any training on carrying out electrical safety checks |
Equipment Type & Construction | Mostly hand-held Class II power tools. There are also some Class I extension reels and each van has a Class I compressor |
Frequency of Use | Hand-held tools and extension reels are moved in and out of the work vans daily |
Electrical Installation | The equipment is mainly used on customers premises, which may not necessarily have circuits with RCD protection. |
Previous Records | PAT testing is currently carried out every 12 months. Records of previous PAT testing show a high percentage of failed equipment. Most equipment is failing due to damaged cables. |
Decision | Previous records show that equipment is regularly failing the visual inspection, so the frequency of formal visual inspections should be increased to every 3 months. The combined inspection and testing should remain at 12 months as the records do not show a history of equipment failing the electrical tests
Previously damaged equipment has only been identified during the annual PAT testing, so in addition, the users should be given training to carry out daily user checks and a system for reporting damaged equipment should be implemented. Hand-held tools should be replaced with battery-powered alternatives, where suitable equivalent tools are available. All remaining tools that can not be replaced with battery-powered equivalents, should be fitted with RCD plugs All Class I and Class II equipment - formal visual inspection every 3 months All Class I and Class II equipment - combined inspection & testing every 12 months |
Office | |
---|---|
Environment | Low Risk. Mostly IT equipment that is very rarely moved. |
User | Staff have been trained to carry out basic safety checks on electrical equipment. Training is updated annually. Staff are not allowed to use personal electrical appliances at work. |
Equipment Type & Construction | Mostly a mixture of Class I and Class II IT equipment. There are also some extension leads, lamps and desktop fans. There are also several Class I heaters that are fixed to the wall and wired to a fused spur outlet. |
Frequency of Use | Daily |
Electrical Installation | All the electrical circuits within the office have RCD protection at the distribution board. The building's fixed wiring is inspected and tested every 5 years. |
Previous Records | PAT testing is currently carried out every 12 months. Previous inspection and test records show no history of any damaged equipment being found. |
Decision | Previous records show that there has been no history of equipment failing during the PAT testing. The staff are diligent at carrying out user checks. The office equipment is rarely moved, so the risk of damage is low. The majority of the IT equipment is regularly replaced every 4 - 5 years. All circuits have RCD protection.
Class I equipment - Combined inspection and testing every three years. Class II office equipment - formal visual inspection every three years, testing not required. Class I wall heaters - To be inspected and tested every 5 years during the inspection and testing of the building wiring. |
There are also a number of similar sample risk assessments available in the IET Code of Practice for In-Service Inspection and Testing, 5th Edition.
HSE guidance
The HSE publish guidance on the frequency of testing and a table with suggested initial maintenance intervals in their publication Maintaining Portable Electrical Equipment.
Guidance on the Initial Frequency of Inspection and Testing
The table below provides some guidance on the initial frequency of the initial inspection and testing. This table is not intended to replace a risk assessment, rather it is intended to help the duty holder decide on a suitable frequency following the risk assessment. This is probably most useful where PAT testing has not previously been carried out, in which case, the table provide a good starting point.
Class I Formal Visual Inspection |
Class I Inspection & Testing |
Class II Formal Visual Inspection |
Class II Inspection & Testing |
|
---|---|---|---|---|
Offices & Shops | ||||
Stationary equipment | 24 months | 60 months | 24 months | none |
IT equipment | 24 months | 60 months | 24 months | none |
Movable equipment | 12 months | 24 months | 24 months | none |
Portable equipment | 12 months | 24 months | 24 months | none |
Hand-held equipment | 12 months | 24 months | 12 months | none |
Fixed | 24 months | 48 months | 24 months | none |
Hotels | ||||
Stationary equipment | 24 months | 60 months | 24 months | none |
IT equipment | 24 months | 60 months | 24 months | none |
Movable equipment | 12 months | 24 months | 24 months | none |
Portable equipment | 12 months | 24 months | 24 months | none |
Hand-held equipment | 12 months | 24 months | 12 months | none |
Fixed | 24 months | 48 months | 24 months | none |
Equipment used by the public | ||||
Stationary equipment | 1 month | 12 months | 12 months | 24 months |
IT equipment | 1 month | 12 months | 12 months | 24 months |
Movable equipment | 1 week | 6 months | 6 months | 12 months |
Portable equipment | 1 week | 6 months | 6 months | 12 months |
Hand-held equipment | 1 week | 6 months | 6 months | 12 months |
Fixed | 12 months | 36 months | 12 months | 36 months |
Industrial including commercial kitchens | ||||
Stationary equipment | None | 24 months | None | 24 months |
IT equipment | None | 24 months | None | 24 months |
Movable equipment | 6 months | 12 months | 6 months | 24 months |
Portable equipment | 6 months | 12 months | 6 months | 12 months |
Hand-held equipment | 6 months | 12 months | 6 months | 12 months |
Fixed | 12 months | 24 months | 12 months | 48 months |
Schools | ||||
Stationary equipment | None | 12 months | 12 months | 48 months |
IT equipment | None | 12 months | 12 months | 48 months |
Movable equipment | 6 months | 12 months | 12 months | 48 months |
Portable equipment | 6 months | 12 months | 12 months | 48 months |
Hand-held equipment | 6 months | 12 months | 12 months | 48 months |
Fixed | 12 months | 36 months | 12 months | 48 months |
Construction sites 110V equipment | ||||
Stationary equipment | 1 month | 3 months | 1 month | 3 months |
Movable equipment | 1 month | 3 months | 1 month | 3 months |
Portable equipment | 1 month | 3 months | 1 month | 3 months |
Hand-held equipment | 1 month | 3 months | 1 month | 3 months |
This table is based on guidance originally published by the IET in the Code of Practice for In-Service Inspection and Testing of Electrical Equipment. It was subsequently removed from the Code of Practice with the publication of the 5th edition. We also provide a copy of the initial frequency table in our training course manual.