Can PAT testing damage the equipment being tested?
The Portable Appliance Testing (PAT) process consists of a visual inspection and a series of electrical tests to determine whether the appliance is safe to use or not. When carried out correctly, PAT testing should not damage the equipment being tested. However, it is possible that incorrect testing procedures could cause damage. To avoid any potential damage, it is important to ensure that the person carrying out the testing is trained and follows the correct test procedures.
Electrical Tests
The specific tests performed will depend on the type of equipment being tested, but the two main ones are the earth continuity test and the insulation resistance test.
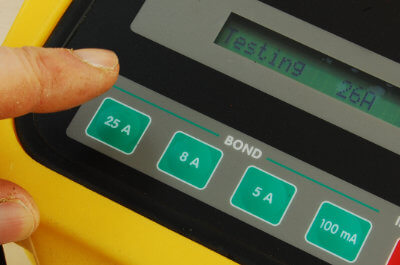
Earth Continuity Test
An earth continuity test is conducted to ensure that a Class I appliance can provide a low resistance path to earth in case of a fault. This test involves passing a current through the earth conductor to measure the circuit's resistance. There are two ways to carry out this test: high current test and low current test.
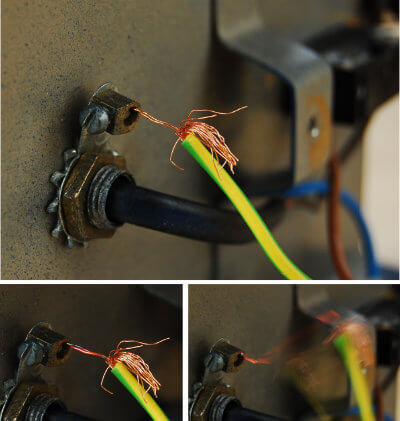
The high current test involves using a current of up to 25A to measure the resistance and check if the conductor is capable of carrying a high current during a fault. It is useful in identifying weak or corroded connections as it can either cause the weak connection to fail or increase the resistance due to heating. However, it's important to note that the high current test isn't suitable for IT equipment or appliances with sensitive electronic components. Electronic circuit boards often use an earth ground as a 0V reference and for screening purposes. Applying a high test current to these parts is likely to damage the electronic components.
In contrast, the low current test uses a test current of between 20mA and 200mA to measure the resistance. Although it doesn't test the integrity of the earth connection in the same way as the high current test, it's highly unlikely to cause any damage to the equipment being tested.
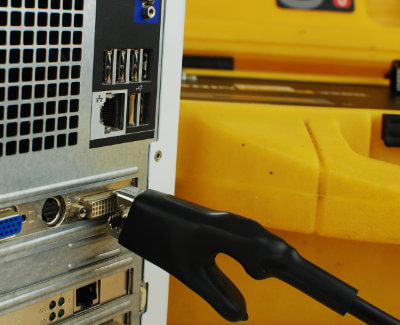
It's essential to select the appropriate test for the equipment being tested to avoid any damage. For instance, IT equipment and appliances with sensitive electronic components should undergo a low current test instead of a high current test. The high current test is suitable for appliances without electronic components, such as extension leads, kettles, heaters etc. The high current test tends to provide a more reliable reading and is less affected by contact resistance.
Most modern PAT test instruments are now battery-powered and can only carry out a low current earth resistance test. This has eliminated the risk of causing any damage to the equipment being tested during the earth continuity test.
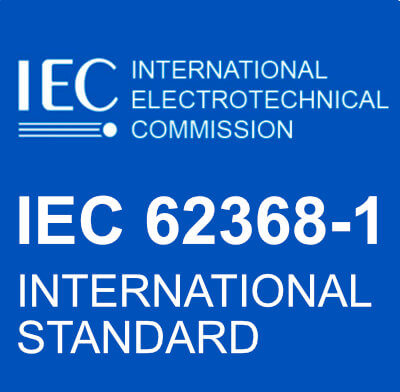
Insulation Resistance Test
An insulation resistance test applies a voltage of 500V between the live conductors and exposed metal parts (Class II), or the protective conductor (Class I). Some older IT or electronic equipment could potentially be damaged by this test. However modern Information Technology Equipment (ITE) is built to EN 60950. This standard outlines specific safety requirements for ITE, including requirements for electrical insulation, earth continuity, and other safety-related tests. The standard requires that equipment should be able to withstand a test voltage of 500V DC for up to one minute. EN 60950 was first introduced in 1992. The standard was replaced in 2014 by IEC 62368-1. The new standard applies to a broader range of audio/video and information technology equipment. For equipment that predates the standard, a reduced voltage insulation resistance test at 250V can be carried out without the risk of damaging the equipment.
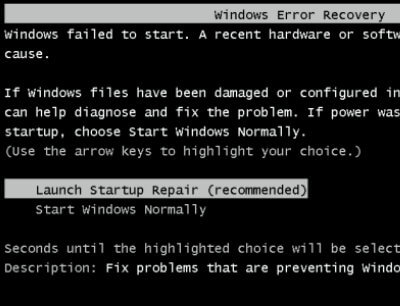
Leakage Test
This test measures the amount of current that is leaking from the appliance to the earth. The test instrument powers up the appliance, usually for around 5 seconds. There is therefore a risk that this could potentially cause mechanical damage, especially as the person carrying out the test may not necessarily be familiar with the correct operation of the equipment. The other potential issue with this test is that starting and stopping IT equipment for just a few seconds can lead to boot errors. As an alternative, a sub-leakage test can be used. This performs a similar test at a reduced voltage, typically 40 - 60 V. Although the sub-leakage test is less accurate, it avoids the problems associated with powering up the appliance.
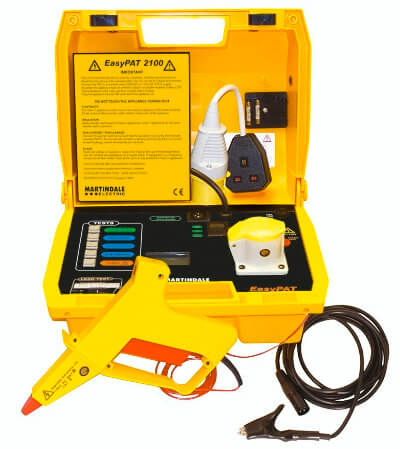
Flash Test
The dielectric strength test commonly referred to as the flash test, applies a high voltage, typically around 1,500V, and measures any current leaking across the insulation. It is important to note that the test is destructive and has the potential to damage the insulation if it fails. The primary purpose of the dielectric strength test is to ensure that the insulation between different conductive parts of the equipment can withstand the operating voltage without breaking down. This test is intended for production testing and testing after repair, and should not be carried out during normal inspection and testing. It is worth noting that some older PAT test instruments do have the function to perform a flash test. It is important to emphasise that the dielectric strength test should only be performed by qualified personnel who have been trained in the proper use of high-voltage testing equipment. Additionally, the test should only be conducted on equipment that is designed to withstand the test voltage to prevent damage to the insulation.
Summary
Selecting the appropriate electrical tests for the equipment being tested is essential to prevent any damage, especially when using older mains-powered test instruments. This highlights the importance of proper training in PAT testing procedures. Our training courses provide this essential education, focusing on correct test selection, use and interpretation of the results.